Explore the world of Concorde with Heritage Concorde
Airframe Production and Construction
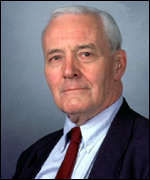
“The Concorde was special, the quality of the work, the minds, the skills, the talent, the commitment that went into it, that’s what really mattered”
Tony Benn former British MP
The construction of Concorde was one of the most complex operations ever undertaken in the aircraft industry. It also represented the first and most important step towards a European aircraft industry, the formation of Airbus.

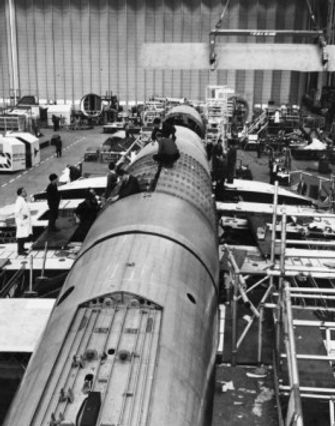
The investment by the British and French governments in research, development and production was vast. Airframe construction was carried out by Aerospatiale (60%) and the British Aircraft Corporation (40%) with engine manufacture divided between Rolls-Royce (60%) and SNECMA (40%).
The main contractors were supported by a large network of sub-contractors, believed to number over 800 in two countries. They ranged from Triplex Safety Glass who made the visors and windows to Hispano-Suiza making the undercarriage. Electronic work was carried out by Elliott and Smiths Industries. Even quite small companies played apart making such things as nylon brackets for the hydraulic pipes and lightweight ashtrays.
Concorde’s long research and development period firmly embraced the whole area of production engineering and management. New methods of machining parts from solid aluminum alloy had been developed, with a massive investment in numerically-controlled machine tools. These could follow intricate blueprints, automatically cutting and milling solid metal blocks. In this way most of Concorde could be put together without joints or welds, which could of become vulnerable under the stresses of supersonic flight. When welding was necessary, new methods using electron beam techniques were press into service.

Concorde’s engineering problems were complex enough, but the task of managing the project was even more demanding. The two main production centres, Bristol (Filton) and Toulouse, were over 600 miles apart, and the factories making everything from wing-tips to seat belts were scattered across Britain and France.
Somehow all the pieces fitted together with infinite precision like a gigantic Meccano set. Teams of liaison engineers backed up by a telecommunications and data network kept the whole machine moving along. Mistakes could have been costly, especially if delays and bottlenecks occurred. All the parts, including large pieces of Concorde’s fuselage, had to be moved across Europe, to their assembly point in Filton or Toulouse. As the pace quickened, the production controllers used a monster Guppy air freighter which looked like a flying whale. These aircraft could carry complete Concorde sections.
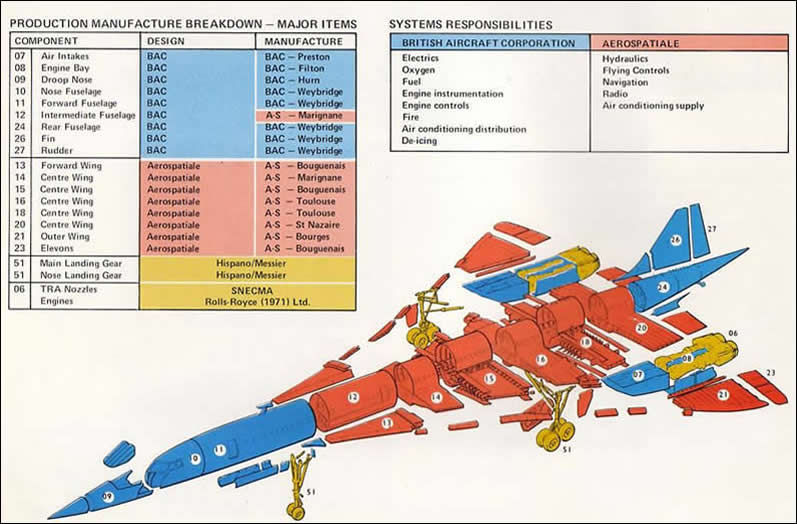
Production of Concorde took place in a number of stages. First there was the assembly of the central fuselage from various sections made at Aerospatiale’s factories at Marignane, Bougenais and Toulouse, together with the nose and tail built at BAC Weybridge. The aluminium parts were fitted together in the assembly hangars at Filton and Toulouse using an overhead crane. A highly important job at this stage was to seal Concorde’s fuel tanks. These were built into the wing, which also contains the wiring for the aircrafts electrical flight control systems. The tanks had to therefore be completely sealed using a chemical, Viton, which could stand the high temperatures of supersonic flight and the inevitable ‘warm up’ of the fuel to over 75c. Concorde’s wings are an integral part of the main fuselage; they were not put on separately as with other aircraft. Only at this point were the leading edges and wing tips added separately, thus completing the famous thin delta.

Once the basic fuselage was assembled, Concorde’s electrical system was then installed. Insertion of 1000’s wires into the narrow fuselage was very difficult task; these were pre-assembled on a gigantic harness which was then hauled into the aircrafts fuselage. When this was completed the airframes elevons, rudder and nose visor attachment were fitted. It was then lifted off the ground on jacks and mounted on its undercarriage, which were still wrapped in polythene at this time to protect the hydraulic mechanism from dust and grease
At this point the power-plant was installed. The Olympus engines, built at Rolls-Royce’s factory at Patchway, were trundled up to the airframe. Before they were secured in position under the wings, the air-intakes and engine bays made at Filton would be checked. These were made of high duty alloy, titanium and stainless steel to withstand the heat that would be generated by the engines running at full blast.
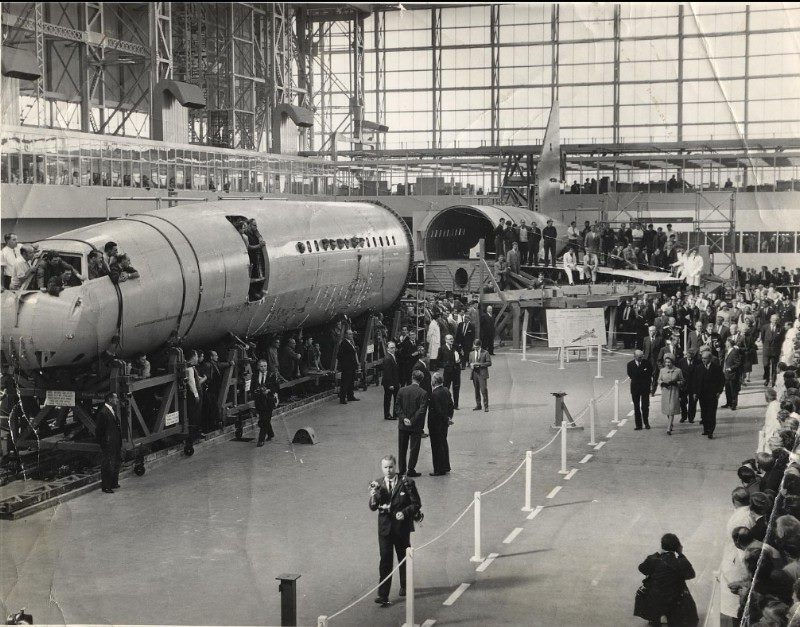
Picture courtesy of Roy Cox
The last main phase of construction began with fitting the nose visor, which had to slide smoothly into place for supersonic flight to protect the flight deck windscreen and streamline the nose. Seals and doors would now be checked for waterproofing and at this stage the Concorde airframe was towed out of the assembly hall to the paint shop where it would become the beautiful white Concorde we all have come to know. Airline insignia would be sprayed on before the final touches are carried out to the aircraft. Flight deck instruments, radio and navigation equipment, together with all the interior trimmings, were the last things to go in. This work would be carried out in the open-air to allow the maximum floor space for assembly inside the main hangars.

Concorde entered service in 1976. 16 production Concorde aircraft were built between 1966 and 1979. Production was carried out in France and in the UK with final assembly at EADS France (formerly Aerospatiale) in Toulouse and BAE Systems (formerly British Aerospace) at Filton. Seven aircraft each were delivered to British Airways and to Air France. One of the Air France aircraft was used for spares and another was lost in a crash in July 2000
In the past, the Concorde manufacturing organisation, and in particular the provision of two separate final assembly lines, one at Filton and the other at Toulouse, has been the subject of adverse comment. Duplication of assembly lines could not be avoided in 1962 however, because it would not have been politically acceptable to have all Concorde’s assembled in one country. Most outside criticism is not, however, directed at the right target – which is the duplication of the “learning curve”, a term that needs a little explanation.

Picture courtesy of Roy Cox
When series production of a new engineering product is begun, everyone concerned has to “learn” how to do his new job. There will be machines to set up, new machining processes to be mastered, jobs to be timed and rates to be fixed. Machinists, fitters, inspectors, supervisors will be feeling their way, and the whole exercise has to be carefully “run in” like a new car.
All this takes time, and, on the production line, time spells money. The first new products off the line, whether they are aeroplanes or washing machines, will cost much more to produce than the price at which they will be sold. That price is based on the assumption that as the workpeople get into the swing of the new job, output will improve and the cost curve will come down steadily until it levels out below the price line. That first downward movement of the curve is called the “learning curve.”
If there are two assembly lines with two lots of people doing the same job, there are obviously going to be two learning curves. To offset the effect of this, BAC and Aerospatiale had made a new approach to aircraft assembly. Up to then, airframe components have been put together on the final assembly jig to form a shell structure, and then all the aircraft systems had been laboriously installed in the shell. In Concorde assembly, much of the work of installing systems was done at the component build stage and the components came, fully equipped, to the final assembly line. This cut down the work of final assembly and moved much of the learning curve out to the sub-assembly where there was no duplication.
One example of such a fully-equipped component is the nose and forward fuselage built at Weybridge, a 50ft.-long section comprising the flight deck, the forward part of the passenger cabin and the nose landing gear bay. When this component was delivered to the final assembly lines, it was equipped with its cabin insulation and the relevant segments of the electrical, hydraulic, flying control and air-conditioning systems, incorporating 25,000 parts and 90 miles of wiring.
Although the basic structural material used in Concorde was an aluminium alloy, titanium and stainless steel were employed in local areas of high stress and high temperature such as the engine bays. Valuable experience has been gained in working with these metals for the future, and advanced manufacturing methods were developed for dealing with the special problems they present.
In aircraft production welding of titanium has proved extremely difficult in the past because the welding heat source, or beam, has to be directed with pinpoint accuracy on to the weld if the strength characteristics of the surrounding metal are not to be adversely affected. Electron beam welding provides this standard of accuracy, and BAC Filton had one of Europe’s largest electron beam welding chambers. Titanium components could be satisfactorily built up by welding, allowing smaller billets to be used and thus saving considerable production cost.
For further information regarding which companies were involved in manufacturing the various parts of Concorde – Click here
Pictures of the Concorde Production Line

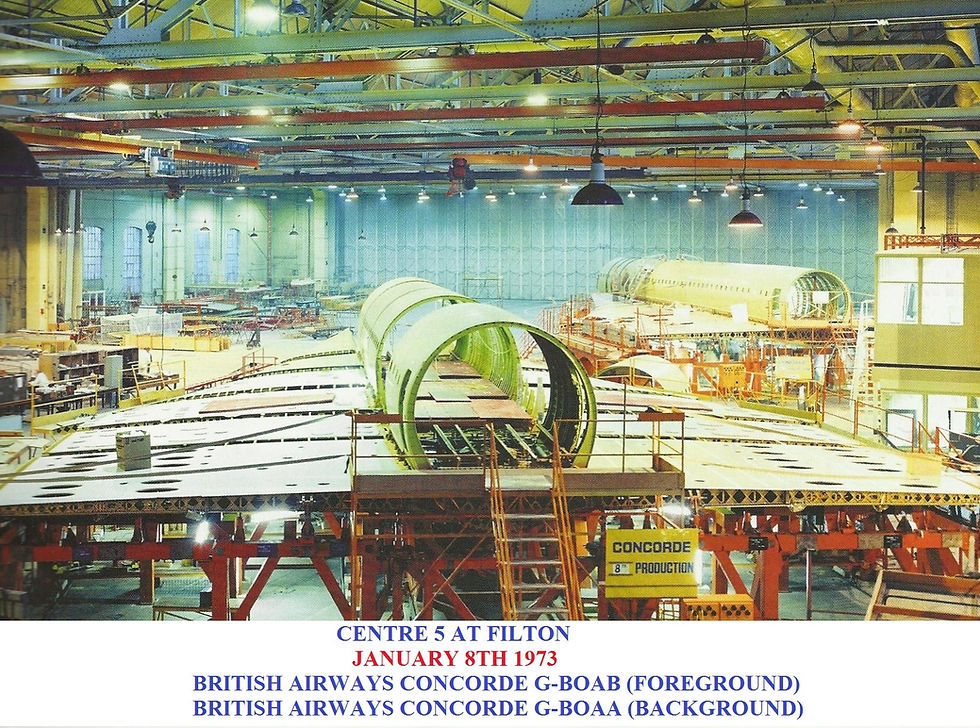

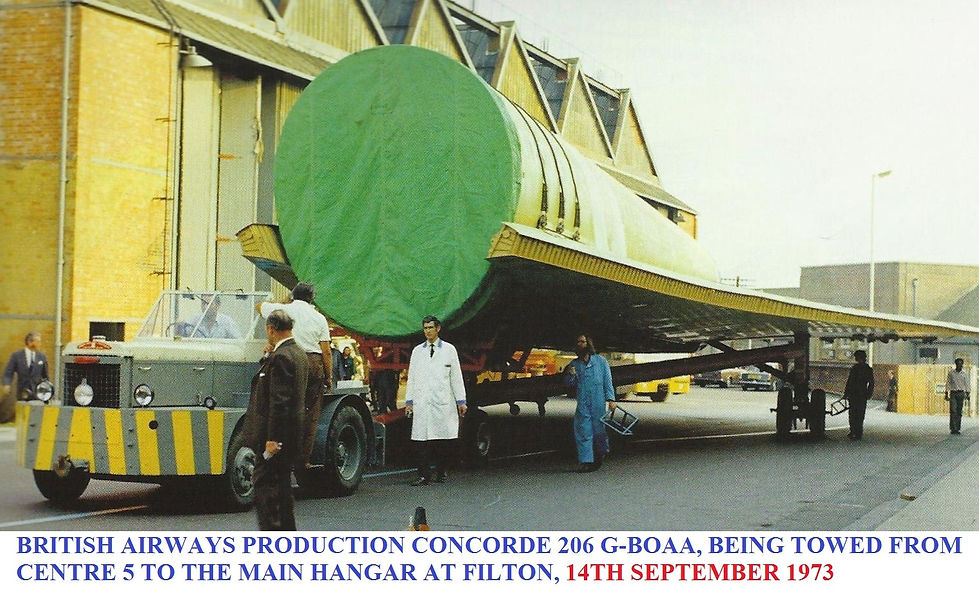


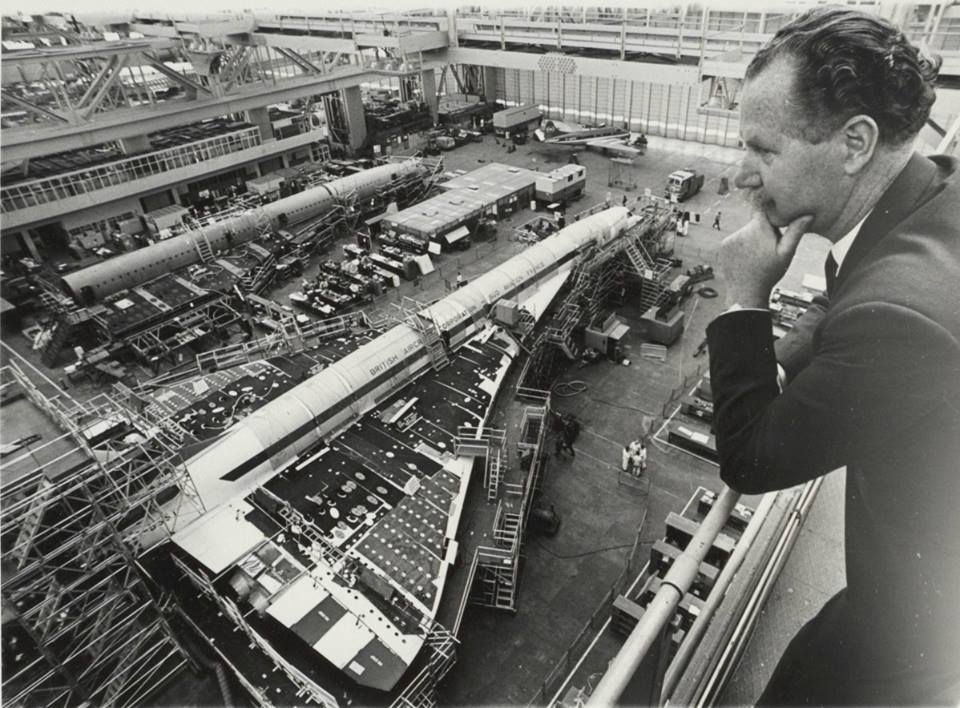