Explore the world of Concorde with Heritage Concorde
Concorde CAA and DGAC Modifications 2001
Background to the Modifications
By summer 2000 Concorde had flown to 250 different destinations around the world. Whenever a Concorde visit occurred she attracted thousands of supporters just wanting to catch a small glimpse of this beautiful, technical miracle. Technically, Concorde was a triumph which can stand alongside the US and USSR space programmes, and way above the Soviet attempts to emulate it.
The dream which began in the minds of a few visionaries way back in the 1950s became the dream of millions of people. For some the dream of flying on Concorde at twice the speed of sound became a reality, but for many it just remained a dream, a burning ambition to experience the thrill of Concorde.
On Tuesday 25th July 2000 at 16.44hrs, just west of Paris-Charles de Gaulle Airport, the dream was shattered as Concorde F-BTSC crashed into a hotel in the Paris suburb of Gonesse, killing 109 people onboard and 4 on the ground.

The crash site at Gonesse, Paris

Concorde Memorial

The words on the Memorial

Concorde F-BTSC on fire
Air France Concorde registration F-BTSC was intended to operate from Paris-Charles de Gaulle to New York-JFK airport the flight was a non-scheduled operation, Flight number AFR4590, on behalf of 100 German tourists en route to a cruise ship. The flight was under the command of Captain Christian Marty, the aircraft began its take-off roll on runway 26 Right. During the take-off a number of sequential problems occurred and although the aircraft became airborne it was neither able to climb above 200 feet nor accelerate beyond 200kts of airspeed. One-and –a-half minutes later the aircraft crashed into a hotel at Gonesses while trying to make for Le Bourget airfield.
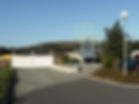
Crash site & memorial to the crew, passengers & the four that died on the ground
Within minutes the BEA set up a team of investigators to try and discover what had happened, and most importantly to see what lesions could be applied in the future. The inquiry process was that outlined in Annex B of the International Civil Aviation Organisation. In accordance with these provisions, the BEA invited participation from the British Air Accident Investigation Branch to join their team, supported by many experts from BAe Systems and Rolls-Royce. Observers from Germany (BFU) and America (NTSB and FAA),and regulators from France and the UK helped to complete the team, which of course included many experts from Air France, EADS owners of Airbus SAS, SNECMA.
Representatives from British Airways and the wheel tyre manufacturers were also included.
The French Ministers of Equipment, Transport and Housing set up a Commission of Inquiry which assisted the BEA in its work and which was informed periodically of its progress. As required by French law, a judicial process was conducted in parallel with the accident investigation.
From the evidence available at the crash site, analysis of components on the runway and data from the various voice and data recorders, the sequence of events is clear. The flight was broken down into three phases:
Phase 1.
From the beginning of the Cockpit Voice Recorded (CVR) recording to the application of take-off power.
Phase 2.
From the application of take-off power to the final lose of thrust on engine number 1.
Phase 3.
Loss of control of the aircraft.
Should Concorde fly again?
Once again this question was asked, those who asked this question were hoping negative answer, as on all previous occasions. The fact is not that none of these who were asking this question were doing their research, nor did they fully understand the implications of cancellation of Concorde, but may be they had another agenda. Once again Concorde champion were needed. The most influential and informed turned out to be Sir Rod Eddington, the new CEO of British Airways PLC. He appeared determined to take Concorde back into service, provided it could be done safely and with the complete confidence of the engineers, crew, manufacturers and regulatory authorities.
Meeting were arranged, technical options evaluated further, and provisional test programmes were drafted just as they had been nearly thirty years before. Concorde would fly again almost regardless of cost.
Concorde was grounded, this section deals with the modifications required to return Concorde to flight following this crash
.
Modifications required to return Concorde to service
CAA & DGAC Airworthiness Directives for Concorde
The following directives were issued to the Airlines and Concorde’s manufactures by the CAA and DGAC on September 5th 2001:
1, The fitment of Kevlar lining to key fuel tanks. –This is to reduce the flow of fuel from any leak which may occur, this together with the removal of electrical ignition sources would make sustained fire impossible.
2, The use of the new Michelin Near Zero Growth (NZG) tyres on all eight main landing gear wheels. – These tyres are designed to be more resilient to damage by foreign objects and only in extreme cases can smaller, lighter tread pieces be released, giving a much lower level of energy on impact than which occurred at Gonesse.
3, The armouring of electrical wiring in the in the main landing gear bay. – The investigators believe that the fire may have been ignited by an electrical spark in the undercarriage bay, and that protecting this area would eliminate the risk.
4, The water deflector retention cable must (if fitted) be removed and there is a slight reprofiling of the deflector to accommodate the new tyres.
5, The antiskid protocols are changed. – This is necessary because of the tyre change. (The anti-skid system is common to most airliners. If an aircraft is about to skid it automatically releases the brakes, for a short time, to prevent a skid developing.)
6, The flat tyre detection and warning system must be working on departure.
7, The electrical power to the brake cooling fans is switched off before take off and landing.
Kevlar fuel tank linings
In order to minimize any fuel leaks, liners have been installed at the bottom of 6 fuel tanks, as configured by the manufacturers. These liners are made of composite fibers Kevlar*, saturated with Viton**, which molds to the shape of the cavities of the panels on the lower surface of the fuel tanks.
* KEVLAR: synthetic fiber developed by Dupont de Nemours, offering maximum resistance to tearing, mainly used in the manufacture of bullet-proof jackets.
** VITON: waterproof sealant, which makes KEVLAR waterproof, used to ensure that the fuel tank structure is waterproof
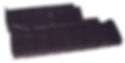


The most time consuming task was the design and manufacture and fitting of the Kevlar fuel tank linings. Thousands of separate, different brackets were needed to fix the linings to the inside of the fuel tanks. Over 100 custom built liners are fitted into each aircraft. Each Concorde is slightly different so many small modifications were needed. The engineers who fitted each piece into the tanks worked many long hours in very difficult physical conditions, but with the same pride and dedication that had always made the Concorde project special. These panels are fitted individually into the tanks and then sealed together to give a fuel tight seal. The Kevlar-rubber panels have been designed to match the density of the fuel (O.792). The installation of these panels would displace some fuel, thus reducing very slightly the overall range of Concorde, but this should not significantly alter the centre of gravity and balance calculations. The centre of gravity of Concorde is of uppermost importance as it is the main method of trimming the aircraft for minimum drag during supersonic flight.

Another important factor that had to be considered was that the fuel is used to cool the airframe and so must still be able to circulate fully on top of and also under the liners.
The liners have small holes in them that would allow the fuel to circulate both above and below the liners. The hole size is a compromise to allow the fuel to circulate correctly but also not to cause any significant flow should a tank be ruptured. Test were carried out on a British Airways owned Rolls-Royce Olympus engine to confirm that the maximum expected flow rate of 0.5L/sec would not have any significant or adverse effect on the engine while running.
Fitting the Kevlar fuel tank linings to British Airways and Air franceConcorde

Manufactures and regulators also played a massive role. This was another ground-breaking task that required ground-test on engines and in-takes, and taxiing trials at low and high speeds. Air France flew to a test base at Istres on a number of occasions, while British Airways consulted on a verification flight programme.
New Tyres
Michelin has produced a new-generation tire especially for Concorde, called NZG (near zero growth).
Its composite material-based* structure has demonstrated considerable resistance to FOD (foreign object damage). In the event of a lost tread or a blowout, the tire bursts in such a way as to project lighter and more flexible fragments.
*COMPOSITE MATERIAL: reinforced fiberglass material used to build structures.
Part-way through the programme, Michelin realised that they could produce a lower profile radial tyre for Concorde; this tyre would be significantly more damage resistant and weigh less than the tyres currently in use. Furthermore if damage, any significant tyre disintegration that resulted in breakaway piece would be much smaller than with the existing cross-ply profile, thereby causing considerably less damage to the wing of landing gear. This new aircraft tire technology, christened NZG for “Near Zero Growth”, uses a high-modulus reinforcement material. This offers higher damage resistance and substantial weight gains, two key qualities in the field of aviation.
“We think that this new tire will be a significant element for the process of re-certification of Concorde “, declared Pierre Desmarets, general manager of aviation activity at Michelin.
These tires were tested on an Air France Concorde (F-BTSD), again at Istres the military test base in the Rhone delta region of France, during a series of ground and flight tests that took place in May 2001.


This development proved to be viable and the new radial tyres were delivered in time for the verification flights. This breakthrough also added to the level of confidence in Concorde, and meant that the Certificate of Airworthiness could be renewed with the full agreement of all concerned.
Modifications to the water deflectors
As the new tire developed by Michelin for Concorde is wider, it was necessary to modifythe geometry of the water deflectors placed on each of the main landing gear.
Other systems were deemed to need modifications to ensure complete compliance with the Regulatory requirements, but these were relatively small when compared to the fuel tanks and tyres changes. They included armour plating for the cabling and hydraulics running through the main gear bays.

The normal operating procedures will be changed so that the 115V supply to the carbon brake cooling fans is deactivated during the takeoff run. It is felt that a short in this supply could have ignited the leaking fuel. These fans can then be turned back on once the undercarriage has been retraced to fully cool the brakes.
British Airways fitted new passenger seats; they weigh less and made up for the weight increase in the fuel tanks.

It is said that British Airways saved over £1 million in fuel per month, due to this seat weight reduction. Everything was completed by the summer of 2001, and on the 16th July British Airways Concorde G-BOAF took off from London-Heathrow Airport on a full supersonic verification flight to RAF Brize Norton in Oxfordshire. The flight was a complete success and on August 15th 2001, the Certificate of Airworthiness was restored, the Concorde dream could live once again!
The new British Airways seats, fitted during the modification.

Concorde G-BOAF on the way to the runway for her first flight to test the modifications

Concorde G-BOAF taking off from heathrow