Explore the world of Concorde with Heritage Concorde
Concorde Green Hydraulic System
Hydraulic power is used to operate those aircraft services requiring a power supply which is substantial and instantaneous, and at the same time meets adequate safety requirements with a minimum of weight. The safety considerations have led to the designers of Concorde to install two independent main systems, known as GREEN and BLUE, together with one more as a back-up system, known as YELLOW, this ensures operation of all vital services during all situations. The same considerations have also determined the number of pumps per system. This section deals with the GREEN system.
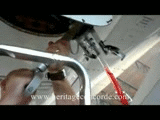
GREEN SYSTEM – DESCRIPTION AND OPERATION
The Green hydraulic system provides the normal power supply to the following services:
-
No.1 and No.2 engine air intakes
-
Normal braking distribution manifold
-
Main landing gear and main landing gear door selectors
-
Nose landing gear and nose landing gear door selectors -
-
Tail landing gear selectors
-
Nose gear steering distribution manifold
-
Visor and droop nose selectors
-
The electro-hydraulic selector for a half-body of each relay jack
-
One artificial feel jack on each of the three axes
-
The electro-hydraulic selector for a half-body of each power flight-control unit (PFCU)
-
The emergency a.c. generator hydraulic motor selector.
-
The fuel transfer pump hydraulic motor selector.
The Green System Includes the Following Components:
-
One hydraulic tank assembly
-
One tank de-aerator safety valve
-
Two heat exchangers
-
Two shut-off valves
-
Two self-regulating engine-driven pumps
-
Three Non-return valves
-
Two low pressure switches
-
Two pulse dampers
-
One Restrictor
-
Two HP micronic filters
-
Two HP filter mounting plates with incorporated non-return valve
-
One Pressure switch (air intake monitoring)
-
HP manifold
-
Pressure relief and manual unloading valve
-
Accumulator
-
Pressure transmitter
-
HP filter
-
Three LP non-return valves
-
Two case drain filters
-
Tank return filter (3 micron)
-
Two system pressurization ground connectors
-
Tank ground filling connector
GREEN SYSTEM TANK ASSEMBLY
The Green hydraulic tank contains the fluid required by the pumps to provide the power necessary for operation of the various aircraft systems.
The Tank Leading Particulars
-
Maximum capacity: 7.1 US gal (S.9 Imp. gallon, 27 litres)
-
Normal fill level: 4 US gal (3.3 Imp. gal, 15 Litres)
-
Low level warning: 1.8 US gallons ~ (1.5 Imp. gallons, 7 litres)
No account is taken of the amount of fluid contained in the bellows when compressed. The amount of fluid not indicated on the indicator is 0.9 US gal (0.747 Imp. gal, 3.4 litres).

The green tank consists of the following…
-
A cylindrical body strengthened by four external stiffeners, and closed at the top by a welded cover and at the base by a bolted plate supporting the bellows.
-
A metal bellows fitted with guides. The hydraulic fluid is contained inside the bellows, whilst pressurizing air acts on the outside.
The following components are mounted on the tank…
-
A de-aerator connected to ambient by a spiral tube.
-
Fluid quantity transmitter with a direct reading indicator.
-
A pressurization non-return valve
-
A direct reading air pressure indicator
-
Low pressure switch (For air pressure)
-
An air pressure relief valve
-
Vacuum relief valve
-
Depressurization valve/sight glass
-
A drain valve
-
An Overheat warning sensor
-
Temperature sensor
.

THE OPERATION OF THE GREEN SYSTEM
Pressurizing air acts upon the outside of the bellows, which contains the hydraulic fluid. As the air and fluid are separated, fluid contamination, emulsion or oxidation is thus avoided. The tank is filled or topped up by means of a hydraulic ground unit which is connected into a tank return line by means of a quick-disconnect self-sealing ground connector, the hydraulic fluid is filtered before entering the bellows. There is a de-aerator which is mounted at the top of the bellows, and which is connected to the bottom of the tank, and then to a deaerator safety valve, by a spiral tube, which in turn provides continuous evacuation through the tube of any air which may have entered the bellows.
There is a fluid quantity transmitter and direct reading indicator assembly which allows for the following…
-
Direct reading of the quantity of fluid in the tank.
-
Electrical transmission to the quantity indicator on the Flight Engineers panel.
-
Control of a microswitch which, when the minimum level is reached results in the following:
Illuminates the L/LEVEL warning light on the Flight Engineer’s panel.
Illuminates the HYD warning light on the master warning panel.
Triggers the aural warning gong.
Shuts off the normal hydraulic power supply to the two associated air intakes.
Automatically switches over the two air intakes to the Yellow auxiliary system.
Discharge of any excess hydraulic fluid in the tank.
A cable connecting the internal mechanism of the quantity indicator to the top of the bellows transmits bellows movement to the indicator.
Pressurizing air is admitted to the tank through a non-return valve.
A low pressure switch calibrated to 29 t 1.45 psi (2 t 0.1 bars) controls the L/PRESS warning light on the Flight Engineer’s panel.
A pressure indicator gives a direct reading of tank air pressure.
A pressure relief valve allows any excess air, which could create tank overpressure, to be vented to ambient.
A vacuum relief valve opens when the pressure differential between the tank and outside pressure reaches 0.34 psi (23 rob).
There is a depressurization valve and sight-glass assembly permits the following…
-
Drainage of condensation water
-
Checking of the bellows for leakage by making certain that there is no fluid in the air compartment
-
Depressurization of the tank, by rotating the knurled control knob.
The green system tank can be drained through a drain valve.
In the event of fluid overheat, a temperature sensor illuminates the O/HEAT caption light on the Flight Engineer’s panel and the HYD warning light on the master warning panel, and also triggers the aural warning gong.
There is also a second temperature sensor that transmits hydraulic fluid temperature information to the Flight Engineer’s panel.
HEAT EXCHANGERS
During flight, heat is generated in the hydraulic system due to internal leakages. To maintain the system fluid at an acceptable temperature, it is cooled in hydraulic fluid/fuel heat exchangers. As a safety precaution hydraulic fluid in the heat exchangers is kept at a higher pressure than the fuel by means of a by-pass valve on the hydraulic fluid line side which opens under the following circumstances occur…
-
Fluid temperature is below 140°F (60°C)
-
The flow rate exceeds 9.25 US gal/rein. (7.7 Imp. gal/rein., 35 litres/minm).
There are two types of heat exchanger:
The type 4 single exchangers which are mounted on engines 1 and 3.
-
(On engine 1 hydraulic pump suction line and fuel supply line)
-
(On engine 3 hydraulic pump suction line and fuel supply line).
The type 3 double heat exchangers
These are formed by coupling two separate exchangers together, one connected to the main system, the other to the Yellow auxiliary system. This type of exchanger is mounted on engines 2 and 4 hydraulic pump suction lines and fuel supply lines. Each of these engines drives two pumps, one for the main and one for the auxiliary system.
Heat Exchanger Construction
Single heat exchanger (type 4):
This consists of a Type 1 core assembly upon which is mounted at one end a moulded housing containing the fuel and hydraulic fluid inlet and outlet ports, and at the other end a cap in AU4G alloy which ensures the transfer of fuel inside, and of hydraulic fluid outside, the core tubes.
A by-pass fitted with a thermostatic valve with incorporated pressure relief valve, is mounted on the housing. The core is made of two brazed light alloy tube assemblies.
Double heat exchanger (Type 3):
This consists of two individual heat exchangers composed of a Type 1 and a Type 2 core, which are mounted on either side of a central moulded support containing the fuel inlet and outlet ports, as well as those of the normal and auxiliary hydraulic systems. It is designed so as to link the core tubes in series, thus providing a single fuel system across the two core assemblies.
The other end of each core bears a cap in AU4G alloy for the fuel and hydraulic fluid transfer from one tube assembly to the other of the same core.
The Engine Driven Hydraulic Pumps

Each pump contains a rotating cylinder barrel, integral with the drive shaft. The barrel houses nine pistons bearing against a yoke by means of shoes which are balanced hydraulically by a thin film of fluid, maintained between the shoes, admitting fluid from the system.
Operation
The rotation of the barrel in relation to the yoke imparts a reciprocating movement to the pistons, which draw in and discharge hydraulic fluid. The tilt angle of the yoke is controlled by an arm driven in one direction by a servo-controlled actuator piston, and in the other by a return piston.
Regulation
Automatic regulation of delivery pressure is achieved by adapting flow to demand, while maintaining a pre-determined pressure of 4000 psi (275 bars).
Delivery pressure is applied to the slide of a pressure compensator valve, which is spring-loaded shut, this spring is adjustable. When delivery pressure exceeds the spring calibration the compensator valve slide is displaced and pressure is admitted to the actuator piston controlling the tilt angle of the yoke. The tilt angle is then reduced, producing a consequent reduction in flow and with the result that the required delivery pressure is maintained. When delivery pressure is below spring calibration, the slide valve closes again and pressure is no longer applied to the actuator piston controlling the yoke angle. The latter is then driven back into the “maximum stroke” position by the return piston.
Depressurization
When the depressurizing solenoid is energized, the delivery pressure is directed to the blocking valve, which then closes the pressure outlet to the delivery line. Movement of this valve creates a new balance in the pressure compensator valve it contains, admitting pressure to the yoke actuator piston, and therefore reducing pump output to zero.
There is no delivery into the system by the pump, but the slight pressure maintained inside it enables lubrication (return is via a case drain).
FILTER ASSEMBLY – TANK RETURN
The filter assembly, which is enclosed in a casing, filters return fluid from the various services and pump case drains. An isolation valve in the filter enables the filter to be replaced, without the tank having to be drained. The main filter consists of 2 parts:
-
An outer part of pleated glass cloth, protected by two perforated plates. The filtering capability of this element, which cannot be cleaned, is 3 microns, absolute.
-
An inner part of nickel-plated wire mesh of 5 microns nominal’ (25 microns absolute) filtering capability. This element can be cleaned.
In the event of accidental clogging the, filter element is protected by four by-pass valves, each of which is equipped with a 13-micron filter. These valves open when the differential between inlet and outlet pressures reaches 13.05 psi (0.9 bars).
The four by-pass valve filters and the three filters on the cover, by-pass the main filter, and enabling evacuation of any air which may accumulate in the filter housing.
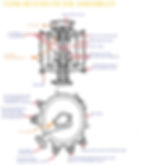
VALVE – PRESSURE RELIEF & MANUAL UNLOADING
In order to ensure smooth operation, the pressure relief valve is adjustable. It contains, in a single housing the following:
-
A pilot slide valve assembly.
-
A distributor slide valve assembly.
The pilot slide valve assembly is an easily removable and replaceable adjustable cartridge. The valve opening pressure is adjusted by means of an adjusting screw on the outside.
The distributor slide valve assembly consists of a sleeve in which moves a slide, controlled by a small actuating cylinder. The unloading device is mounted at the end of the distributor slide valve and it comprises of the following…
-
A housing attached to the pressure relief valve
-
A plunger piston
-
A cam attached to a spindle. A control lever is attached to the protruding end of the spindle.
The Operation
For system pressure between O and 4583 psi (O to 316 bars), (opening pressure setting) the displacement of the pilot slide valve does not allow supply to the distributor slide valve actuating cylinder. The system under pressure is closed. When a pressure of 4583 psi (316 bars) is reached, the connection to the distributor slide valve opens. However, in order to ensure smooth operation of the pressure relief valve, the pilot valve is designed as a pressure reducing valve. The servo pressure acting on the distributor slide valve actuating cylinder depends on the actuating cylinder spring calibration.
The system opens gradually by a relatively long piston stroke. This design avoids any distributor slide valve vibration, and consequent uneven operation of the pressure relief valve.
VALVE – TANK DE-AERATOR – SAFETY
The de-aerator safety valve connects the tank de-aeration outlet port to ambient, thus enabling continuous de-aeration of the hydraulic fluid. The valve consists of housing with a bore at the top in which a float-valve rises and falls.
Operation
In the event of any failure of the tank de-aerator, hydraulic fluid fills the body of the safety valve and lifts the float. The needle valve on the end of the float closes the port.
Beneath the float a spill chamber prevents the valve being closed by any globules of liquid.
TANK DE-AERATOR SAFETY VALVE
Operation
The components composing the Green system have the following functions:
The hydraulic tank supplies fluid through heat exchangers and shut-off valves, to two self-regulating hydraulic pumps. These supply the various services with hydraulic fluid at 4 000 psi (275 bars) pressures, via micronic filters and non-return valves.
(A free-moving piston-type hydraulic accumulator installed at the manifold absorbs pressure surges and provides the extra pressure required to compensate for pump response time, when a substantial, instantaneous power supply is required for the services or servo-control units.
The hydraulic tank is pressurized to 65 psi (4.5 bars) in order to avoid pump cavitation. Its maximum volume is 7.1 US gal (5.9 Imp. gal, 27 litres) and its normal fill quantity is 4 US gal (3.3 UK gal, 15 litres). Any drop in pressurizing air pressure, any fluid overheats or low level conditions are indicated on the Flight Engineer’s HYDRAULIC MANAGEMENT panel on the flight deck.
The hydraulic fluid/fuel heat exchangers incorporated in the suction line enable fluid temperature in the system to be kept at an acceptable level of 203 to 221”F (95 to 105”C). The exchangers operate when fluid temperature exceeds 140°F (60”C) or when pump output is less than 9.25 US gal/rein. (7.7 Imp. gal/min=Y 35 litres/min.).
In the event of an engine fire, shut-off valves on the suction line, located in the wing outside the nacelle, cut off the hydraulic fluid supply. Each valve is operated by an electric motor controlled by a 3-position ON, OFF, SHUT switch on the Flight Engineer’s panel:
-
ON, OFF position: shut-off valve open
-
SHUT position: shut-off valve closed.
The SHUT position can only be obtained after the sealed guard on the switch has been raised. In the event of an engine fire, actuation of the relevant ENG FIRE handle causes the shut-off valve(s) to close. A magnetic indicator on the Flight Engineer’s panel shows the position of the shut-off valve (OPEN or SHUT). During valve transit the de-energized indicators cross-hatched.
The two self-regulating pumps driven by engines 1 and 2 accessory gearboxes supply a pressure of 4000 psi (275 bars) and can provide a nominal delivery of 34.34 US gal/rein. (28.60 Imp. gal/rein., 130 litres/ min.). Circulation of recuperated return leakage ensures cooling and lubrication of the pump. Each pump has a solenoid-controlled depressurizing system. The solenoid is energized by the three-position ON, OFF, SHUT switch on the Flight Engineer’s panel:
-
In ON position the solenoid is not energized, and the pump is pressurized
-
In OFF or SHUT position the solenoid is energized and the pump depressurized.
A magnetic indicator on the Flight Engineer’s panel indicates whether the pump is pressurized or depressurized (it displays ON or OFF respectively).
The suction, delivery and case drain hoses are composed of two concentric reinforced pipes. The hydraulic fluid normally flows through the inner pipe. In the event of leakage it passes into the outer pipe. A mechanical check device fitted on the hose connection enables the condition of the inner pipe to be checked.
On the pump HP delivery hose any fluid leakage in the inner pipe is drained off into the pump suction Line. Pulse dampers installed on hydraulic pump delivery lines reduce pressure surges in magnitude.
There is a pressure switch which is preset to 2030.5 psi (140 bars) and which is mounted in parallel with the delivery line of each pump to indicate any pump failure. A non-return valve prevents any back pressure on the pump should the engine or the pump itself shut down. It also maintains the pressure of the other pump in the system.
Delivery pressure signals are transmitted to an indicator on the Flight Engineer’s panel by a pressure transmitter mounted in parallel with the servo-control selector supply line. A pressure relief and manual unloading valve preset to 4583 psi (316 bars), and mounted on the manifold, protects the system from excess pressure due to thermal expansion of the fluid, or to a malfunction of the pump regulation system.
The manually actuated unloading device enables the hydraulic system to be depressurized during ground maintenance or trouble shooting work. All services and pump case-drain returns to the tank pass through non-return valves and a 3-micron filter. A valve fitted on each LP and HP filter allows the filter element to be removed without the tank having to be drained.
The system is self-bleeding and no special bleeding procedure is required when equipment is changed. Pressurization of the system and a component functional test are sufficient to eliminate any air in the system.
The tank is filled on the ground through a ground connector and an LP filter. Two ground connectors incorporating self-sealing valves enable system pressurization and testing to be carried out using ground power units.
Self-sealing valves enable rapid disconnection of the hydraulic lines during removal of an engine.
ELECTRICAL POWER SUPPLY
Power is supplied to the control and indicating circuits by the essential busbars.